Coil Thickness Optimization for Better Steel Slitting Results
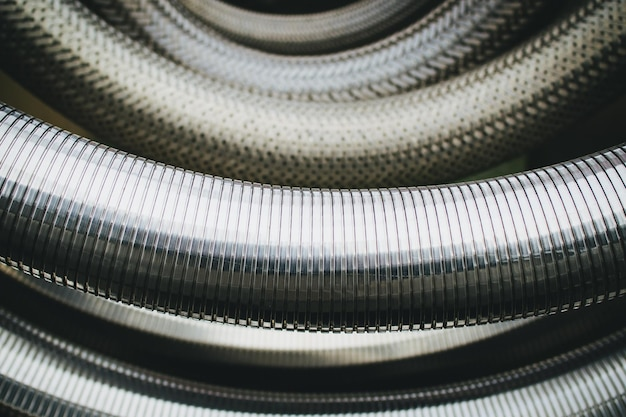
Understanding Coil Thickness in Steel Slitting
Coil thickness plays a pivotal role in the steel slitting process, influencing both the efficiency of operations and the quality of the final product. The thickness of the coil not only determines the type of machinery required but also affects the cutting precision and the overall performance of the slitting line.
The Importance of Coil Thickness
Coil thickness impacts several aspects of slitting operations:
- Cutting Precision: Thicker coils can be more challenging to cut accurately, as they require more powerful machinery and sharper blades. In contrast, thinner coils are generally easier to slit but may bend or warp if not handled correctly.
- Material Properties: The thickness of the coil can influence its mechanical properties. Thicker materials tend to have higher tensile strength, which can affect how they respond to cutting forces.
- Cost Efficiency: Optimizing coil thickness can lead to significant cost savings. Thinner coils may reduce material waste and energy consumption during the slitting process, while thicker coils might offer better value in terms of strength and durability.
Factors Influencing Coil Thickness Selection
When selecting the appropriate coil thickness for slitting, several factors should be considered:
- End-Use Requirements: Different industries have varying specifications for coil thickness based on their application. For example, automotive components may require thicker materials for durability, while appliances might utilize thinner gauges.
- Slitting Equipment Capabilities: The type of slitting machine in use will dictate the range of coil thicknesses that can be effectively processed. High-speed slitting lines are typically designed to handle a variety of thicknesses, while some machines are optimized for specific gauges.
- Material Type: The type of steel being processed can also influence the choice of thickness. For instance, high-strength steels may necessitate thicker coils to achieve desired performance characteristics.
The Slitting Process: How Thickness Affects Performance
The slitting process involves cutting wide coils into narrower strips, and the thickness of the coil plays a crucial role in determining the effectiveness of this operation.
Loading and Feeding
The initial step in the slitting process involves loading the coil onto a decoiler. The thickness of the coil can affect how it is handled during this stage:
- Weight Considerations: Thicker coils are heavier, requiring robust cranes and handling equipment to load them safely.
- Tension Management: Proper tension is essential for accurate slitting. Thicker coils may require more precise tension control to prevent deformation during the cutting process.
Cutting Mechanism
The cutting mechanism is where coil thickness significantly influences the outcome:
- Blade Selection: Thicker coils typically require specialized blades designed for high strength and durability. Using inappropriate blades can lead to poor cutting performance and increased wear.
- Cutting Speed: The speed at which the coil is fed into the slitting line can vary based on thickness. Thicker materials may necessitate slower feed rates to ensure clean cuts.
Post-Slitting Operations
After the slitting process, the thickness of the coil can impact subsequent operations, such as:
- Edge Treatment: Thicker coils may require additional edge trimming to ensure a clean finish, while thinner strips can often be packaged directly after slitting.
- Packaging and Shipping: The weight and dimensions of the final product will depend on coil thickness, influencing storage and transportation logistics.
Optimizing Coil Thickness for Enhanced Quality
To achieve the best results in steel slitting, optimizing coil thickness is essential. This can be accomplished through various strategies.
Assessing Material Requirements
Before determining the optimal thickness, it is crucial to assess the specific requirements of the end application. This involves:
- Consulting Industry Standards: Understanding the standards for thickness within the target industry can guide the selection process.
- Engaging with Customers: Collaborating with customers to understand their needs can provide insights into the appropriate thickness for their applications.
Testing and Feedback
Implementing a testing phase can help refine the thickness selection process:
- Trial Runs: Conducting trial runs with different thicknesses can provide valuable data on performance and quality.
- Gathering Feedback: Collecting feedback from operators and customers can help identify any issues related to thickness and inform future adjustments.
Continuous Improvement
The optimization of coil thickness should be an ongoing process:
- Monitoring Trends: Keeping an eye on industry trends can help anticipate changes in thickness requirements.
- Investing in Technology: Upgrading slitting machinery to accommodate a wider range of thicknesses can enhance operational flexibility and efficiency.
The Role of Technology in Coil Thickness Optimization
Advancements in technology have revolutionized the steel slitting process, enabling more precise control over coil thickness.
Automated Slitting Lines
Modern automated slitting lines are equipped with sophisticated features that enhance the ability to manage coil thickness effectively:
- Real-Time Monitoring: Sensors can provide real-time data on thickness, allowing for immediate adjustments during the slitting process.
- Automated Blade Adjustment: Some machines can automatically adjust blade positions based on the thickness of the coil, improving cutting accuracy.
Advanced Material Handling Systems
Innovative material handling systems also contribute to better thickness management:
- Precision Feeding Mechanisms: These systems ensure that coils are fed into the slitting line with the correct tension, regardless of thickness.
- Enhanced Decoiling Equipment: Advanced decoilers can accommodate a range of coil thicknesses, reducing the risk of damage during loading.
Training and Operator Skills
The expertise of operators is a critical factor in optimizing coil thickness during slitting operations.
Comprehensive Training Programs
Investing in thorough training programs for operators can significantly improve the handling of various coil thicknesses:
- Understanding Equipment: Operators should be well-versed in the capabilities and limitations of the slitting machinery to make informed decisions about thickness.
- Best Practices: Training should include best practices for loading, feeding, and monitoring coils of different thicknesses to minimize errors.
Continuous Skill Development
Ongoing education and skill development can further enhance operator performance:
- Workshops and Seminars: Regular workshops can keep operators updated on the latest techniques and technologies related to coil thickness optimization.
- Feedback Mechanisms: Establishing feedback channels allows operators to share their experiences and insights, fostering a culture of continuous improvement.
Quality Control Measures
Implementing robust quality control measures is essential for ensuring that coil thickness meets specifications throughout the slitting process.
Regular Inspections
Conducting regular inspections of both the coils and the slitting equipment can help identify any issues related to thickness:
- Visual Checks: Operators should perform visual inspections to detect any irregularities in coil thickness before slitting.
- Measurement Tools: Utilizing precise measurement tools can ensure that the thickness of the coils aligns with industry standards.
Documentation and Reporting
Maintaining thorough documentation of thickness measurements and quality control checks is crucial:
- Tracking Trends: Documenting thickness data over time can help identify patterns and inform future decisions.
- Reporting Issues: Establishing a reporting system for thickness-related issues can facilitate prompt resolution and improvement.
Environmental Considerations
Optimizing coil thickness is not only beneficial for operational efficiency but also for environmental sustainability.
Waste Reduction
By selecting the appropriate thickness, companies can minimize material waste during the slitting process:
- Efficient Use of Resources: Thinner coils may lead to less scrap material, contributing to more sustainable practices.
- Recycling Opportunities: Excess material from slitting can often be recycled, further reducing environmental impact.
Energy Efficiency
Managing coil thickness can also enhance energy efficiency in slitting operations:
- Lower Energy Consumption: Thinner coils typically require less energy to process, leading to cost savings and reduced carbon footprint.
- Optimized Machinery Usage: Investing in machines designed for specific thicknesses can improve energy efficiency and overall performance.
Economic Impacts of Coil Thickness Optimization
Optimizing coil thickness can have significant economic implications for steel suppliers and consumers alike.
Cost Savings
Implementing effective thickness optimization strategies can lead to substantial cost savings:
- Reduced Material Costs: By minimizing waste and optimizing material use, companies can lower their overall material costs.
- Improved Productivity: Efficient slitting operations result in faster turnaround times and increased output, enhancing profitability.
Competitive Advantage
Companies that prioritize coil thickness optimization may gain a competitive edge in the market:
- Meeting Customer Demands: Being able to offer customized thickness options can attract more customers and foster loyalty.
- Enhancing Reputation: Commitment to quality and efficiency can enhance a company’s reputation in the industry, leading to increased business opportunities.
Future Trends in Coil Thickness Optimization
As the steel industry continues to evolve, several trends are emerging that will shape the future of coil thickness optimization.
Advancements in Materials
The development of new materials may influence coil thickness requirements:
- High-Strength Alloys: The introduction of advanced alloys could enable thinner coils without sacrificing strength, altering traditional thickness standards.
- Lightweight Materials: As industries seek to reduce weight in applications, there may be a shift towards thinner materials, necessitating adjustments in slitting operations.
Technological Innovations
Ongoing technological innovations will further enhance the ability to optimize coil thickness:
- Artificial Intelligence: AI-driven systems could analyze data to suggest optimal thicknesses based on historical performance and market trends.
- Smart Manufacturing: The integration of smart manufacturing technologies may enable real-time adjustments to slitting operations, improving efficiency and quality.
Conclusion
Optimizing coil thickness is a critical aspect of achieving superior results in steel slitting operations. By understanding the implications of thickness on cutting performance, investing in technology, and prioritizing operator training, companies can enhance their efficiency, reduce waste, and improve product quality. As the industry evolves, staying attuned to trends and advancements will be essential for maintaining a competitive edge. Embracing these strategies will ensure that steel suppliers meet the diverse needs of their customers while promoting sustainability and economic viability in their operations.